全国地磅电子秤销售、维修电话158-8101-1465





自动称量配料系统图目录
自动称量配料系统图
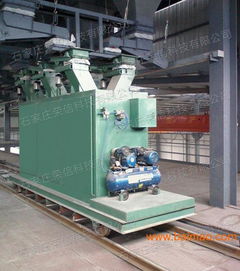
自动称量配料系统图
一、系统概述
自动称量配料系统是一种高效、准确的自动化配料解决方案,广泛应用于化工、食品、制药等领域。该系统通过集成原料存储、配料秤、配料管路、混合器、输送带、控制系统、安全保护装置、废料处理设施以及监测与记录系统等功能模块,实现了从原料入库到成品出库的全流程自动化。
二、主要组成模块
1. 原料存储区
原料存储区是自动称量配料系统的起始点,用于存储各种原料。该区域配备了通风和除湿设备,以确保原料的品质和存储安全。同时,该区域还配备了自动化的物料搬运设备,如叉车和堆垛机,以实现高效存储和出库。
2. 配料秤
配料秤是自动称量配料系统的核心组成部分,用于精确计量各种原料。该设备采用高精度的称重传感器和先进的控制算法,确保计量结果的准确性和稳定性。同时,配料秤还配备了自动标定和校准功能,以确保设备长期运行的可靠性。
3. 配料管路
配料管路是连接各原料存储区和配料秤的管道系统,用于传输原料。该管路系统采用不锈钢材料,具有防腐、防泄漏等特点。同时,配料管路还配备了各种阀门和过滤器,以实现原料的灵活控制和过滤。
4. 混合器
混合器是自动称量配料系统的关键设备之一,用于将各种原料按照预定的配方进行混合。该设备采用先进的混合技术和控制算法,确保混合结果的均匀性和稳定性。同时,混合器还配备了冷却和加热装置,以满足不同工艺的需求。
5. 输送带
输送带是连接各设备和工位的传送装置,用于将原料、半成品和成品从一个工位输送到另一个工位。该设备采用高强度、耐磨的材料制成,具有可靠的传输能力和稳定性。同时,输送带还配备了智能化的控制系统,以实现自动化输送和跟踪。
6. 控制系统
控制系统是自动称量配料系统的“大脑”,负责整个系统的协调和控制。该系统采用可编程逻辑控制器(PLC)或工业计算机(IPC)作为主控单元,通过各种传感器和执行器实现对各个设备的精准控制。同时,控制系统还具备友好的人机界面(HMI),方便操作人员进行监控和操作。
7. 安全保护装置
安全保护装置是自动称量配料系统的重要组成部分,用于保障设备和人员的安全。该装置配备了各种安全传感器和紧急停止开关,当发生异常情况时能够迅速响应并采取相应措施。同时,安全保护装置还具备可编程逻辑控制功能,以实现个性化定制和安全防护。
8. 废料处理设施
废料处理设施是自动称量配料系统中必不可少的部分,用于处理生产过程中产生的废料。该设施配备了各种废料处理设备和环保设施,如废气处理装置、废水处理装置等,以确保废料的妥善处理和环保达标。同时,废料处理设施还具备智能化的监控和管理系统,以实现废料处理的自动化和可持续性。
9. 监测与记录系统
监测与记录系统是自动称量配料系统中用于数据采集、分析和记录的子系统。该系统通过各种传感器和仪表实时监测各设备的运行状态和工艺参数,并将数据传输到控制系统进行集中处理和记录。监测与记录系统的数据可用于后续的生产分析和品质追溯,有助于提高生产效率和产品质量。
影响plc控制系统稳定性的因素有哪些
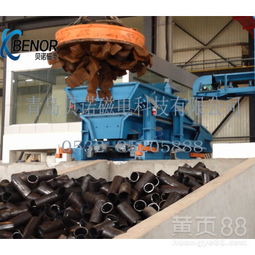
1.前言
饲料称量包装的准确与否将直接影响到企业的信誉和经济效益。
过去采用机械称量、人工装袋,劳动强度大、速度慢、精度低。
近几年,采用电子称量装置虽然可使其静态称量精度大大提高,但在饲料加工连续生产过程中,其动态精度仍不能保证。
因此,在快速自动称量中如何提高动态称量精度,一直是饲料加工企业急需解决的难题。
本文是作者在研制饲料自动化生产设备中,为了与配料过程相协调,实现饲料生产的全部自动化,应用PLC作为动态称量包装测控设备,在硬件和软件设计中采用了一些措施和动态控制方法,较好地兼顾了称量速度与精度的矛盾,实现了饲料连续生产中动态称重计量的精度。
2.系统总体框图及工作原理
用称重传感器、放大器和PLC组成测控系统来完成饲料的称重、计量、包装的生产工艺过程,如图1所示。
该系统以PLC为核心,配以称重传感器、放大器、各种电动执行器和机械装置,实现饲料的动态在线称重计量和包装工作。
称斗的上方是成品仓,该仓中的原料是来至饲料混合工序生产的饲料散状成品料。
成品仓下是一台电动机驱动的螺旋进料装置,启动电动机,则该成品仓中的粉状饲料就随着传输绞笼的旋转而进入称斗中称量。
称斗上装有三个S梁式应变式拉力传感器,称斗的重量信号直接由该传感器组转换成与之对应的电压信号,经放大器把该电压信号放大后送入PLC中进行数据处理,当达到预定值时,PLC控制停止下料,然后PLC控制开称斗门,并控制打包机自动装袋后由传送带送出。
于是,就完成了饲料称量打包的自动化过程。
3.提高动态称重精度的硬件措施
该系统用三个拉力传感器将饲料重量W变换为成线性关系的电压信号Ux,并通过两级放大器进行放大。
图中Un表示等效到放大器输入端的噪声和干扰电压,ΔUi表示等效到输入端的漂移电压。
设两级放大器的放大倍数为A,则Uo=A(Ux+Un+ΔUi)=AUx+AUn+A·ΔUi式中的第2项主要影响灵敏度,第三项主要影响系统的精度。
(1)影响传感器的因素及解决办法
传感器输出信号的稳定性除决定传感器本身的性能外,还与供电电源和传感器的安装有密切关系。
本系统采用UH61-100u型三只称重传感器,每只传感器单独供电,通过调节其桥路电压使三只传感器的输出灵敏度K相同,三只传感器串联输出的电压为Ux=K(E1+E2+E3)。
为了提高每个传感器供桥电源的稳定性采用二次稳压,并对元器件进行老化、测试后进行选配,特别是对基准稳压管2DW233的老化处理和时漂测试,选择时漂小的通过调节其工作电流使其工作在接近零温度系数(<2ppm/℃)下,使整个传感器电源的温度稳定性优于10ppm/℃。
三只拉力传感器安装在称斗和称架之间。
如果传感器承受的重量与传感器轴线存有ɑ角,则将产生横向分力而引入误差ΔW=W-Wcosɑ.这对于每次称重25Kg,在称斗皮重为100Kg的情况下,即三只100Kg的传感器实际荷重为125Kg。
当ɑ=4°时,称重误差就为0.43Kg。
因此,安装传感器时应设法确保传感器都能垂直受力。
(2)影响系统灵敏度的因素及解决办法
影响系统灵敏度的主要因素是检测电路的内部噪声和外部干扰电压Un,它与放大器所工作的频带相关。
在研制中,通过选择低噪声器件,在满足采集速度所需足够宽的频带的前提下,通过选配电阻来提高放大电路本身的共模抑制能力,整个检测系统采用双层屏蔽,采样时间选为工频周期整数倍等项措施,使整个系统获得了能分辨5g重量的灵敏度。
(3)影响准确度的主要因素及解决办法
影响准确度的主要因素是整个检测系统的非线性和漂移ΔUi。
其中系统的非线性,在选配元器件校正的基础上,采用了软件修正;而对于随温度和时间产生的漂移电压ΔUi,主要采用元器件的老化、测试与分选工艺,筛选掉时漂大的,然后选配温度系数进行补偿,使整个系统的静态精度达到了0.07%,为实现动态称量精度奠定了基础。
4.提高动态称重精度的软件措施
影响动态称重精度的主要因素是被称物料的比重、流量和落差的大小,它是由成品料仓的压力和PLC所控制的进料驱动装置产生的。
因此,改进控制思路,借鉴静态称量精度高的特点是提高动态计量精度的关键。
为此,我们选用双速变径变距螺旋加料机,采用"先快后慢,最后点动"的控制下料方式,如图2所示。
图中:Wx0为称量前PLC所采集的称斗皮重;由此PLC按照每包计量净重量的90%、95%和100%算出快速下料的终了值Wx1、慢速下料终了值Wx2和称量终了值Wx。
其控制过程可以这样简单说明:在下料开始一段时间,PLC控制绞笼电动机快速下料,当检测达到快速下料的终了值Wx1时,PLC控制绞笼电动机开始慢速下料;当检测达到慢速下料的终了值Wx2时,PLC关闭绞笼电动机后采用"点动"下料,当达到或接近期望值Wx时为止。
按照上述思路,通过编写全动态控制加料的快慢、速加料和点动下料的软件模块;以及为消除空中落料对称量精度的影响,所编写的自动寻找提前停机量的软件模块等软件措施。
该系统使用一年来,经计量部门两次测试,整个系统动态计量准确度优于0.2%。
5.结论
采用PLC控制进行饲料称重包装,具有结构简单、计量准确、工作可靠,较好的兼顾了动态称重计量的精度和速度,满足了在线快速动态重量计量的要求,对水泥、食盐、面粉等的称重包装有借鉴作用和推广价值。
原文网址:
自动配料系统的作用是什么?
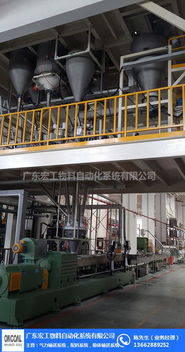
自动化配料称重系统被广泛用于食品、药品和化学材料中,如调味料、活性成分和催化剂。
这些自动化控制系统,使制造商能够增加产量,减少劳动力和材料的变化。
这些自动化系统还简化了批量跟踪和生产记录的保存。
随着生产过程自动化水平的提升,称重传感器已是生产过程控制中不可或缺的一个必要装置。
称重传感器现在已经覆盖了所有的称重领域,从料斗、料罐称重到汽车衡、起重机等称重均可实现,自动配料称重到粉体颗粒进量控制等也都可以通过称重传感器实现。
高精度称重传感器或称重模块可用于工业现场在线计量及配料控制,为更方便地接入工业测量控制系统中,可提供多种规格的称重变送器。
亦可提供专门的配料控制器用以完成罐装包装、配料等生产过程连续自动化运行或控制。
在工业生产控制中,由于机器需要长时间连续运转,这对设备的可靠性就有着极高的要求。
称重传感器需满足这一需求,可靠性高,抗干扰能力强,防雷性能好。
可实现不间断工作,节约停机启动时间;维护方便,系统整体成本低等特点。
配料称重系统是由称重传感器,称重仪表,控制系统的结合,达到对罐体的称重计量工作,从而进行控制的系统。
称重及控制系统主要由多只称重传感器,多路接线盒(含放大器),显示仪表,输出多程控制信号组成。
该系统可应用于各种箱体称重,罐装液体,固体称重及干粉搅拌机,砂浆配料搅拌机,液体配料罐等。
用户可以直接接入PLC系统、终端控制系统、实现多程控制及自动化控制.
PLC自动配料系统模拟设计
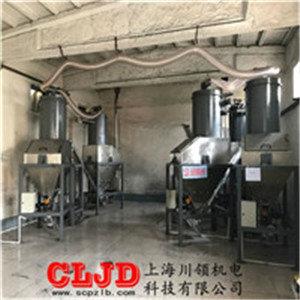
系统启动后,配料装置能自动识别货车到位情况及对货车进行自动配料,当车装满时,配料系统能自动关闭.
工作过程
(1)出使状态
系统启动后,红灯L2灭,绿灯L1亮,表明允许汽车开进装料,料斗出料口D2关闭,若料位传感器S1置为OFF(料斗中的料物不满),进料阀开启进料(D4亮),当S1置为ON(料斗中的物料已满),则停止进料(D4)灭,电动机M1,M2,M3和M4均为OFF
(2)装车控制
装车过程中,当汽车开进装车位置时,限位开关SQ1置为ON,红灯信号灯L2亮,绿灯L1灭.同时启动电机M4.经过2S后,再启动M3,再经过2S后启动M2,在经过2S最后启动M1,再经过2S后才打开出料阀(D2亮),物料经料斗出料.
当车装满时,限位开关SQ2为ON,料斗关闭,2S后M1停止,M2在M1停止2S后停止.M3在M2停止2S后停止,M4在M3停止2S后最后停止,同时红灯L2灭,绿灯L1亮,表明汽车可以开走.
(3)停机控制
按下停止按纽SB2,自动配料装车的整个系统终止运行.