全国地磅电子秤销售、维修电话158-8101-1465





配料称重系统参数目录
配料称重系统参数

配料称重系统的参数主要包括精度、量程、滤波设定、校准、数据输出方式和流量与计量控制等。
1. 精度和量程:称重传感器的精度和量程需要根据实际需求进行选择。精度需要符合实际要求,而量程则需要根据系统的需求来确定,同时还需要考虑称重台面的大小和材质等因素的影响。
2. 滤波设定:称重值的滤波设定是保证系统稳定性和精度的关键因素之一。滤波器的应用可以消除传感器的噪声干扰,滤波设备的参数设置可以根据不同的环境需求进行调整,以达到合适的滤波效果。
3. 自动校准和手动校准:自动校准和手动校准能够提高称重精度和系统的可靠性,但需要注意参数的设定和跟踪。不同的称重传感器在安装和运行时,都需要进行初始校准和定期校准,手动校准时要遵守正确操作规程,避免误操作造成的电子设备的破坏。
4. 数据输出方式:数据输出方式的设定包括串口、以太网、USB 接口等方式。这些接口的设定需要根据实际需求进行设置,同时还需要考虑串口输出的范围、速度和可靠性等因素对于数据输出的影响。
5. 流量和计量控制:流量和计量控制是称重配料系统的主要控制参数之一。计量控制需要根据不同应用场合中的流量变化来调整参数,以确保精度和稳定性。而流量控制则可以根据不同的工艺特性进行调节,实现更加精确的计量。
此外,还有一些特定设备的参数需要考虑。比如对于粉体配料称重系统,可能还包括人工上料方式、出料方式(如采用震动送料器)、密封方式(如料仓和震动器之间采用软密封)以及配方控制加料方式(如采用顺序控制)等参数。
以上内容仅供参考,如需更专业的信息,建议咨询配料称重系统方面的专家或查阅相关文献资料。
配料系统怎么提高配料精度?有哪些可行的方法?

1、顺序配料较为常用,各种物料按照设定的配方顺序加和称量斗中,任何时候只允许一种物料加入称量斗中。
称重控制设备检测称量物料重量的变化,并控制相应各物料仓的放料门,及称量料的出料门。
使用称重模块,称重终端即可构成净重式定量控制系统。
用户可以从称重终端输入各种配方,也可以上位PC机下载各种配方。
2、对于一些不允许进行隙式的顺序配料工作的场合,或者要求连续工作的场合,可采用连续配料方式。
各种物料分别称重,并同时按照设定的流量加入混料中混合。
使用称重模块,多只称重终端即可构成连续配料系统。
用户可以从称重终端输入各种配方,也可从上位PC机下载各种配方至称重终端。
扩展资料
配料系统的主要功能
1、监控功能:对皮带称配料过程的瞬时流量、日累计、月累计、年累计等参数进行检测和监视。
2、画面显示:通过计算机显示器可显示配料过程中有关控制参数的运行状况,以及显示实时配料曲线和表格。
3、打印管理:可随时打印配料报表,以便保存和查询。
4、通讯功能:与PLC和仪表之间进行可进行双向数据及信息交换。
5、数据处理:配料系统可自动对采集的信号进行运算处理,并输出到相应的控制量。
6、控制功能:根据操作前相应的设定值,自动控制设备的正常运行,包括PID调节。
7、报警功能:上位机以画面方式和声光信号方式对各种参数超限或设备状态异常进行报警。
参考资料来源:
参考资料来源:
GM8804A称重配料控制器怎么标定最好详细
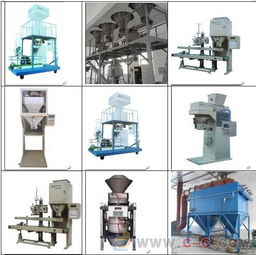
展开全部
调 校
用户在初次使用GM8804A配料控制器,或者称重系统的任意部分有所改变,以及当前仪表参数不能满足用户使用要求时,应对仪表进行调校,具体说明如下:
把标定开关拨到“ON”位置,然后打开仪表电源,则仪表进入调校状态。
任何时候,把标定开关拨到“OFF”位置,仪表都将结束调校返回暂停状态。
调校时主显示为仪表出厂时的原设定参数值,或为上一次所设定的参数值,副显示为调校内容的提示符号。
如果用户只想改变某一参数,那么在完成改变后,把标定开关拨到“OFF”位置,仪表将存储这一改变并返回暂停状态。
调校方法
步骤 调校内容 调校方法及有关说明 显示
第一步 把标定开关拨到“ON”位置,打开仪表电源,显示保留1秒后,自动进行第二步
第二步 重量单位 若不改变重量单位,进行第三步;否则用“+,--”键选择。
注:重量单位共3种,参见12页
第三步 按“确认”键,进行第四步
第四步 小数点位置 若不改变小数点位置,进行第五步,否则,用“+,-”键选择。
注:小数点位置共5种,参见12页
第五步 按确认键,进行第六步
第六步 最小分度 若不改变最小分度值,进行第七步,否则,用“+,--”选择。
注:最小分度有6种,参见12页
第七步 按确认键,进行第八步
第八步 最大量程 若不改变最大量程,进行第九步,否则改变最大量程,方法参见第12页
注:最大量程≦最小分度Χ10000
第九步 系统检测 按“确认”键,副显示:从12倒计数00后显示“St”,主显示:秤斗自重W0传感器输出的毫伏数N0.
Δ若进行系统检测,待主显示稳定后记N0,进行第十步。
Δ若不进行系统检测,跳到第十八步
第十步 检测传感器输出信号,
Δ若N0=W0*B*12/A,进行第十一步
Δ否则,进行第十七步 A: 传感器额定量程
B:传感器灵敏度
第十一步 按“清零”键,进行第十二步,主显示变为零。
第十二步 系统检测 把重量为W的砝码放在秤面上,显示稳定后,记录下主显示毫伏数 N1.
第十三步 按“清零”键,进行第十四步,主显示变为零。
第十四步 再把重量为W的砝码放到秤面上,显示稳定后,记 主显示毫伏数N2.
第十五步 若 N1=N2=W*B*12/A, 则传感器及传力机构工作正常,否则进行第十七步。
第十六步 卸去所有砝码,按“退出”键,
Δ若主显示毫伏数=N0,进行第十八步
Δ否则进行第十七步
第十七步 检查传感器及传力机构,并进行相应的调整后,返回第十步。
第十八步 按“确认”键,副显示“CO”, 主显示为传感器输入信号。
Δ若进行零位标定,进行第十九步
Δ否则,按“退出”键跳到第二十步
第十九步 零位标定 按“确认”键,主显示:0,零位标定完成副显示为CA,进行增益标定。
* 稳定灯亮才能进行零位标定。
* 主显示:“OVER”,说明传感器输出信号太大
* 主显示:“UNDER”说明传感器输出信号太小
第二十步 若不进行增益标定按“退出”键,直接跳到第二十四步,否则,进行第二十一步
第二十一步 增益标定 将接近最大量程(一般大于最大量程的80%)的标准砝码放在秤台上,主显示稳定后稳定灯亮,进行第二十二步。
注:主显示, 传感器加载后输入信号
第二十二步 按“确认”键,主显示:0,并从高位开始闪烁,进入输入状态。
第二十三步 输入标准砝码重量值,按“确认”键确认,若无误,则完成增益标定; 否则自动返回第二十一步
第二十四步 把标定开关拨到“OFF ”位置,主显示“HELLO” 变为称重显示, 副显示从12倒计数至00,系统进入暂停状态
标定参数
符 号 参 数 种 类 参 数 值 初 始 值
Un 重量单位 3 1(g) 2(kg) 3(t) 1
Pt 小数点位置 5 0 0.0 0.00 0.000 0.0000 0
1d 最小分度 6 1 2 5 10 20 50 1
CP 最大量程 ≦最小分度X 10000 10000
自动配料系统组成及特点有哪些?

自动配料系统以微机为中心,结合强电设备组成闭环系统。
测试对象是电子秤的重量信号,各种开关量的输入信号、控制对象是给料机、秤斗闸门、混合机闸门和油脂添加开关阀等机电装置。
不同的自动配料系统能达到的指标不同,但其最基本要求是:静态配料精度≤0.1%;动态配料精度≤0.3%;可以存贮一定数目的配方,不受断电影响;有准确的报警信号;每一生产工段具有连锁保护功能,能连续生产;生产中,具有断电保护功能和误差自动修整功能;接收和发送信号有自动检测功能;具有静态精度标定测试功能;具有自动、手动切换工作功能。
在实际生产过程中,配料系统可分成三个过程组成:配料过程、混合过程、混合机排料过程。
自动配料系统的中心环节就是配料秤,在配料时按照生产配方要求,由生产控制应用程序自动控制配料,由所需各种料相应料仓绞龙分别下料,秤斗重量产生的变化经计算机采集得到,当所需料量达到设定值时转到下一种料配置。
当各种料都配置完后,此时配料过程结束,而如混合机中无料,且混合机门关紧和混合机主机工作时,开启秤斗门,料落入混合机中进入混合过程。
如果需要油脂添加和微量组分添加,则分别启动它们,可自动添加,也可示警提示。
当混合达到设定混合时间后,则开启混合机门并自动计时时,进入混合机排料过程。
按照混合机排料速度设定开门时间,当达到设定开门时间时关闭混合机门。
这样就完成了一次自动配料。
同时,上述三个过程不是孤立工作,而是有机结合的。
混合机混合料的同时,配料秤也在同时配料,保证配料工段和混合工段的不脱节,确保自动生产的连续性。