全国地磅电子秤销售、维修电话158-8101-1465





自动配料系统模拟实验目录
自动配料系统模拟实验

自动配料系统模拟实验
一、系统架构概览
自动配料系统主要由以下几个部分组成:原料存储、输送系统、配料比例设定模块、配料顺序控制模块、实时监控与调整模块、异常处理机制以及实验结果评估模块。这些模块协同工作,确保配料的准确性和效率。
二、原料存储与输送
原料首先被储存在指定的存储设施中,这些设施通常是封闭的,以防止原料受到污染或变质。然后通过输送系统,原料被输送到配料区。输送系统通常由传送带、提升机和其他相关设备组成,确保原料按照预设的顺序和时间输送到配料区。
三、配料比例设定
配料比例是生产过程中重要的参数,直接影响到产品的质量和性能。通过预设的比例参数,配料系统可以自动控制原料的添加量,确保产品的稳定性。比例设定的准确性对于产品的质量控制至关重要。
四、配料顺序控制
配料顺序同样影响产品的质量和性能。通过精确控制原料的添加顺序和时间,可以确保产品的均匀性和稳定性。顺序控制模块通过预设的程序,精确控制各原料的添加时机,提高生产效率。
五、实时监控与调整
为了确保配料的准确性和一致性,系统会实时监控配料的进程。如果发现实际配料比例或顺序与预设参数有偏差,系统会自动调整,确保生产过程的稳定。此外,监控系统还可以记录生产数据,为后续的质量控制和优化提供依据。
六、异常处理机制
七、实验结果评估
最后,通过对实验结果的评估,可以全面了解自动配料系统的性能。评估内容包括但不限于:配料准确度、生产效率、设备稳定性以及操作便捷性等。根据评估结果,可以对系统进行优化和改进,提高生产效率和产品质量。
PLC自动配料系统模拟设计
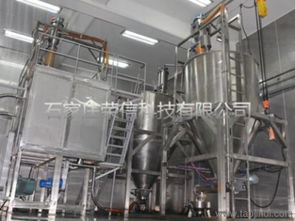
系统启动后,配料装置能自动识别货车到位情况及对货车进行自动配料,当车装满时,配料系统能自动关闭.
工作过程
(1)出使状态
系统启动后,红灯L2灭,绿灯L1亮,表明允许汽车开进装料,料斗出料口D2关闭,若料位传感器S1置为OFF(料斗中的料物不满),进料阀开启进料(D4亮),当S1置为ON(料斗中的物料已满),则停止进料(D4)灭,电动机M1,M2,M3和M4均为OFF
(2)装车控制
装车过程中,当汽车开进装车位置时,限位开关SQ1置为ON,红灯信号灯L2亮,绿灯L1灭.同时启动电机M4.经过2S后,再启动M3,再经过2S后启动M2,在经过2S最后启动M1,再经过2S后才打开出料阀(D2亮),物料经料斗出料.
当车装满时,限位开关SQ2为ON,料斗关闭,2S后M1停止,M2在M1停止2S后停止.M3在M2停止2S后停止,M4在M3停止2S后最后停止,同时红灯L2灭,绿灯L1亮,表明汽车可以开走.
(3)停机控制
按下停止按纽SB2,自动配料装车的整个系统终止运行.
小料自动配料的生产过程
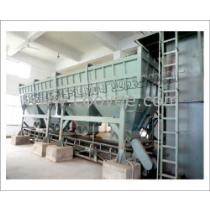
小料车间直接读取追溯系统或ERP系统的生产任务单和生产配方进行配料,每批配料时先扫描产品条码,然后根据配料顺序提示扫描原料条码和投入原料,直到配方中所有需要配料的原料全部配料完成,提示将计量桶拿走,准备下一批配料可联系159 8987 6873基本原理就是这样子的。
自动配料系统组成及特点有哪些?
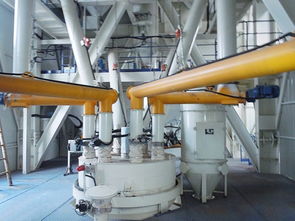
自动配料系统以微机为中心,结合强电设备组成闭环系统。
测试对象是电子秤的重量信号,各种开关量的输入信号、控制对象是给料机、秤斗闸门、混合机闸门和油脂添加开关阀等机电装置。
不同的自动配料系统能达到的指标不同,但其最基本要求是:静态配料精度≤0.1%;动态配料精度≤0.3%;可以存贮一定数目的配方,不受断电影响;有准确的报警信号;每一生产工段具有连锁保护功能,能连续生产;生产中,具有断电保护功能和误差自动修整功能;接收和发送信号有自动检测功能;具有静态精度标定测试功能;具有自动、手动切换工作功能。
在实际生产过程中,配料系统可分成三个过程组成:配料过程、混合过程、混合机排料过程。
自动配料系统的中心环节就是配料秤,在配料时按照生产配方要求,由生产控制应用程序自动控制配料,由所需各种料相应料仓绞龙分别下料,秤斗重量产生的变化经计算机采集得到,当所需料量达到设定值时转到下一种料配置。
当各种料都配置完后,此时配料过程结束,而如混合机中无料,且混合机门关紧和混合机主机工作时,开启秤斗门,料落入混合机中进入混合过程。
如果需要油脂添加和微量组分添加,则分别启动它们,可自动添加,也可示警提示。
当混合达到设定混合时间后,则开启混合机门并自动计时时,进入混合机排料过程。
按照混合机排料速度设定开门时间,当达到设定开门时间时关闭混合机门。
这样就完成了一次自动配料。
同时,上述三个过程不是孤立工作,而是有机结合的。
混合机混合料的同时,配料秤也在同时配料,保证配料工段和混合工段的不脱节,确保自动生产的连续性。